How It Works
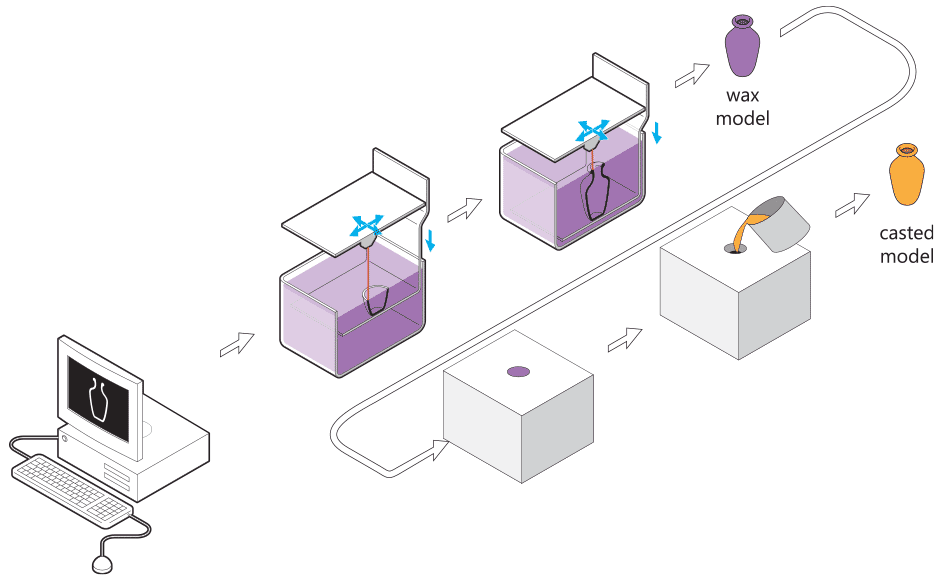
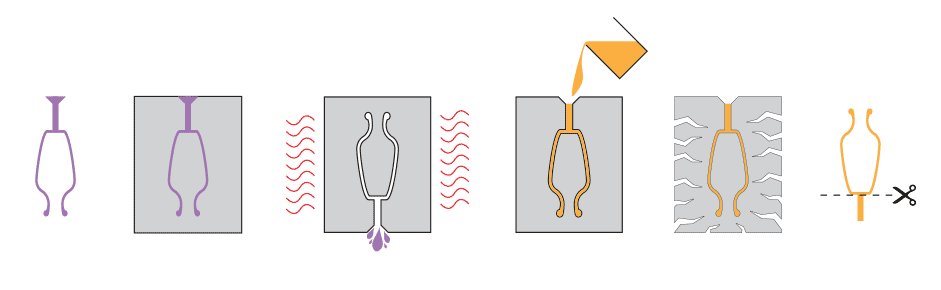
Wax 3D printing and lost wax casting are used to build your design when using this material. The wax printing process is a type of stereolithography that uses a wax-like resin. Support structures are printed along with the model to make sure your model doesn’t fall apart. These support structures are automatically generated and manually removed after the printing process. After support structures are removed and your model is cleaned, the model can be prepared for casting.
First, one or more wax sprues will be attached to your model. Next, it will be attached with the sprue to a wax ‘tree’, together with a bunch of other models. The tree is then placed in a flask and covered in a fine plaster. When the plaster solidifies, it forms the mold for casting the metal. The plaster mold is then put in an oven and heated for several hours to a point where the wax is completely burned out.
Then, the molten metal is poured in to fill the cavities left by the wax. Once the metal has cooled and solidified, the plaster mold is broken and the metal models are removed by hand. Finally, your model is filed and sanded to get rid of the sprues. It will be sanded, polished or sandblasted for the finish you desire.
Materials
Gold
- 14K or 18K solid Gold
- Mainly used for precious jewelry
- The material is mixed with an alloy for hardening for longer ware
Silver
- Solid Sterling silver, made of 92.5% pure silver and 7.5% of another metal
- Very high electrical and thermal conductivity
- Very malleable
- Mainly used for jewelry and ornamental items
Bronze
- An alloy consisting primarily of copper
- Affordable
- Mainly used for jewelry, detailed miniatures, and sculptures
- Oxidates or tarnishes if not PU coated or varnished
Brass
- An alloy of copper and zinc
- A more economical replacement for precious metals
- Mainly used for jewelry, pre-print tests (e.g. to form-fit before ordering Gold or Silver), detailed miniatures and sculptures
- Oxidates in a greenish way if not plated or varnished
Copper
- 100% pure copper
- Very high thermal and electrical conductivity
- Corrodes in a greenish way if not varnished or coated. The varnish or coating will slow down the oxidation but won’t prevent it in the long run.